Production of screen-printed overlays is a highly complex and specialized process. Attention to detail is essential in every stage from order entry to shipping the final product.
Order Entry
The first part of the process—order entry—establishes the groundwork for the rest of the procedure. During this stage, materials, inks, pricing and scheduling are entered into a database. An order is then generated and specialized internal paperwork is printed and submitted to the Prepress Department. It is here that the preliminary artwork is transformed into fully functional production art files.
Artwork
All artwork submitted to the Prepress Department goes through stages of development based upon the type(s) of file(s) submitted and the complexity of the part being produced. From these files, an Art Master is generated in Adobe Illustrator, an industry-standard vector-based program that serves as a bridge between the simple drawing and files that can be used for production. The Prepress Department must take into account the number and types of inks involved, materials, any artwork that may be deemed problematic on press, and die complexity.
Once the Art Master is complete, it is emailed to the customer for approval. At this point, any potential problems are addressed. Once the artwork is approved, production files can be set up and films can be output. Ideal Jacobs uses a thermal-based film in order to reduce the environmental impacts that can normally be found in a traditional chemical-based film output environment. Each film represents at least one color. Films are also output for die making purposes.
At this point, production paperwork is generated that summarizes the materials and inks to be used, quantities required, ship date, and production notes that serve to aid in either the printing or finishing of the overlays. Paperwork is also generated for the Die Making Department that summarizes the materials in use, the film setup, the number of dies (or electronic files needed for laser cutting) required for that job, and the ship date. From Prepress, films and paperwork are taken to the appropriate departments for production. |
|
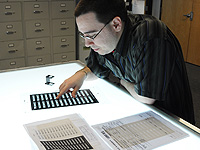
Once artwork is approved it is reviewed by the Prepress Department before it is taken to the screen-making area. |
Die Making
In the Die Making Department, each film is used to create a different die. The film is applied to a piece of 5/8" thick plywood using adhesive supplied on rolls. Various cuts are then made to the die board in order to accommodate the cutting steel. The steel is bent and cut in specialized jigs that are mounted to a sturdy workbench, then installed by aligning the steel to the appropriate cuts in the board and lightly tapping it in with a hammer equipped with a soft plastic head. Special rubber is then applied to the board that ejects the overlay from the face (or cutting side) of the board. The die is now ready for production.
Depending upon such factors as complexity, demand, or speed, the job may be selected for cutting by our state-of-the-art laser cutter. A DXF file is generated by the Prepress Department and then sent to the Laser Cutting Department where all necessary offsets and compensations are made to provide the most accurate finished part. With the use of a laser cutter Ideal Jacobs is able to produce parts that, in the past, were beyond the capabilities of a steel rule die or hard tooling. The laser cutter allows Ideal Jacobs to meet the demanding tolerances of today’s manufacturing environment.
Screen Making
Roughly at the same time that the dies are being created, screen making takes place. A completed screen is composed of a metal or wood frame, polyester mono high modulus screen mesh, mounting hardware, and a photosensitive stencil that produces an image on the screen when it is exposed to ultraviolet light. The stencil is applied to the screen by baking it to the surface in a large oven. This allows the Mylar layer to be removed from the screen without damaging the stencil. A film is mounted to the screen with cellophane tape, then placed on a vacuum table (to prevent shifting of the film on the screen and to produce the sharpest possible image), then exposed to an ultraviolet light source for a predetermined amount of time. The non-image area is then washed from the screen and allowed to dry. Once completely dry, the screen can be used for printing.
Press / Production
The production staff will take the completed screens, one at a time (based on the ink order), and mount them to the printing press. At the same time, the material is converted from full sheets to a more efficient size based on the image area of the job at hand (from this point on, this material is known as a press sheet). Before each press sheet gets placed onto the press to be printed, it is passed through a cleaning machine that lifts any excess debris and static from the surface of the sheet, ensuring a clean, printable surface.
The first press sheet is then placed on the vacuum table at the front of the press, under the screen. It is aligned to ensure proper registration to the proceeding colors. Ink is then applied to the screen in an even layer. Excess ink is removed and placed back into the proper ink container. (Ideal Jacobs uses UV-sensitive ink to reduce environmental impact).
As each ink and sheet is printed (known as an impression), it is mechanically removed from the vacuum table with an arm known as a take-off, which places it on a conveyer that carries the press sheet to the exposure unit at the end of the press. The exposure unit consists of a set of ultraviolet lamps and fans that help to dissipate heat buildup. As the ink passes under the lamp, it is cured, making the press sheet ready for inspection and the next ink, if applicable. After the first impression is complete, the process is repeated from mounting the next screen to the press through final inspection of the printed press sheets.
Once a screen is no longer needed for production, it is returned to the Screen Making Department, where the image is removed, thus making the screen available for another job. When all printed press sheets are complete, they are placed in a specified area for finishing.
Die Cutting & Finishing
While printing is taking place, members of the production staff will prepare adhesive and alternate materials (if necessary). This involves obtaining the dies necessary from the Die Making Department. If an overlay requires selective adhesive—i.e., non-adhesive area for an LED—a specific die is used to cut the adhesive beforehand. The selective adhesive is applied by hand to ensure proper alignment. Non-selective adhesive is applied directly from a roll. In either case, the press sheets with adhesive are sent through a laminator, which applies pressure to the combination of materials in order to remove air bubbles. Once the adhesive is applied and/or final assembly is complete, the overlays are ready to be die-cut.
In the die-cutting process, the dies that finish the part are mounted to a clamshell press, which applies force to the cutting edges on the face of the die, thus finishing the part. Alignment guides are applied to the base of the clamshell, allowing for consistent cutting of each part. Scrap material is used for initial alignment testing to avoid damaging good press sheets. Once alignment is complete, press sheets are placed on the base of the clamshell individually, where the clamshell closes, then opens to reveal the finished part. The finished parts are stacked until die-cutting is complete. Once all press sheets are cut, they are transferred to the Quality Control Department for cleaning and inspection. |
|
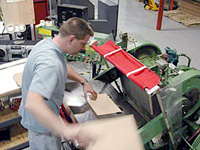
After printing, adhesive is applied to press sheets which are later die-cut using a clamshell press. |
Quality Control
All excess material is stripped from press sheets. Strict guidelines for inspection are followed to check for any printing and/or die cutting and dimension inconsistencies. Specific attention is paid to sensitive areas that can impact performance of the part. Any rejected parts are isolated and counted to determine the percentage of unusable parts and to establish if a non-conformance should be generated.
Shipping Department
Product is counted and weighed and packaged in specific quantities in anti-static bags and packed in appropriate boxes. Bar codes and any additional customer requirements are entered for each shipment and shipped according to customer instructions. Once the shipment is entered in the computer tracking information is emailed to the customer. Products are shipped worldwide from our US Headquarters. |